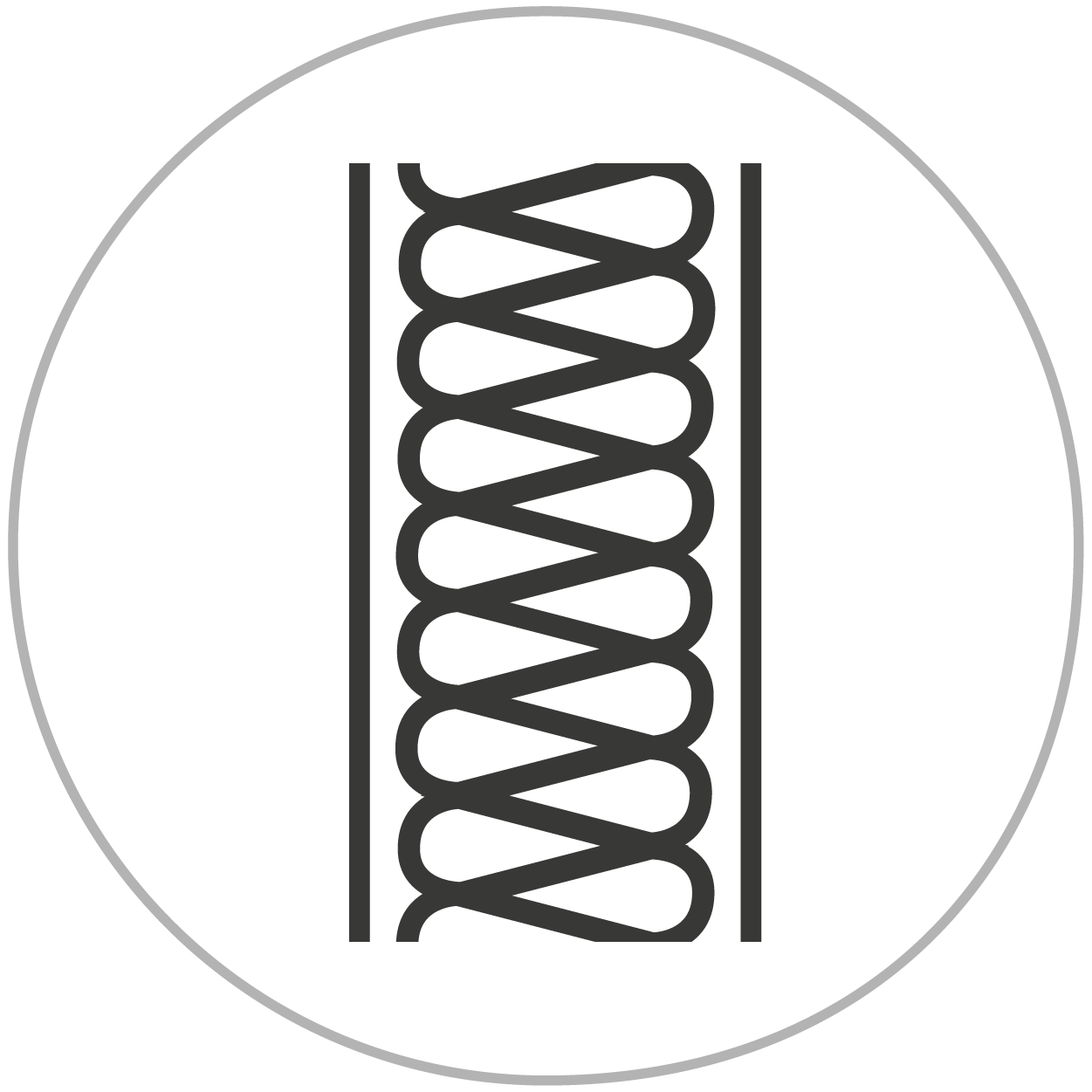
Insulation Product Guidance
Use the red-to-green product guidance below to select safer product types by avoiding those in red and preferring yellow and green, which are safer for occupants, fenceline communities, and workers.
When choosing insulation:
- Prefer products that are based on natural materials, recycled cellulose, or minerals. Good options include cork, wood fiber, sheep’s wool, hemp, and certain fiberglass and mineral wool.
- Avoid plastic foam insulation, whether board or spray-applied.
- For board insulation, prefer expanded cork, wood fiber, and unfaced formaldehyde-free fiberglass or mineral wool.
- Blown and batt insulations are generally good options from a material health perspective, but pay attention to binders and facers. See below for the best blown and batt options.
- Avoid products with formaldehyde-based binders and those with flame retardant facing materials.
- Use mechanical installation methods, such as fasteners, to avoid unnecessary use of adhesives.
Insulation is a very broad product category that employs a variety of material types, such as cellulose, glass and mineral fiber, plastic foam, and natural materials that are used in a range of forms—batt, blown, sprayed, and board. It is an important component of almost all new construction and many energy-efficiency improvements. Given the quantity of insulation used, it is easy to see how material decisions can cumulatively affect the amount of toxic material brought into building spaces.
Insulation products can contain a range of hazardous chemicals. Those of highest concern include halogenated flame retardants, formaldehyde-based binders, and isocyanates reacting on site. These chemicals can impact installers as well as building occupants.
In addition, the production of insulation materials can also have significant impacts on nearby communities and the broader environment through the release of hazardous chemicals. These impacts can occur at the facilities that make the insulation products as well as those farther back in the supply chain. For example, some insulation is made primarily of plastic or other petroleum-derived materials. Oil and gas extraction and processing have significant impacts on surrounding communities.[1]
Here is some additional, more detailed guidance to use when choosing insulation materials:
- Prefer insulation products that are based on natural materials, recycled cellulose, or minerals. Good options include cork, wood fiber, sheep’s wool, hemp, and certain fiberglass and mineral wool.
- Some of these materials may be more expensive than other product types or have limited availability in some regions, requiring advanced planning. Commonly used fiberglass and cellulose insulations are some of the best ranked from a health perspective and have the lowest installed cost per given R-value. While the R-value per inch is higher for many foam products, the R-value per dollar is not.[2] The same insulative performance can be achieved with these healthier materials for applications with few space restrictions.
- Avoid plastic foam insulation, whether board or spray-applied. Foam insulations commonly contain toxic flame retardants, and spray foam contains asthma-causing isocyanates. These products are also petroleum-based and can have significant impacts on communities throughout the manufacturing process. See Chemical and Environmental Justice Impacts in the Life Cycle of Building Insulation for more information. If foam insulation must be used, avoid products that are reacted on site, like spray foam. Also, look for products that do not use halogenated flame retardants. In order to achieve insulation and air sealing, while avoiding spray polyurethane foam, use a combination of lower hazard sealants (such as acrylic caulk or foam sealant tape) and insulation (such as fiberglass or cellulose).
- For board insulation, prefer expanded cork, wood fiber, and unfaced formaldehyde-free fiberglass or mineral wool. These products avoid or mostly avoid petroleum-based chemicals and do not contain halogenated flame retardants or formaldehyde-based binders.
- Blown and batt insulations are generally good options from a material health perspective, but pay attention to binders and facers. Most blown and batt insulation avoids the chemicals of greatest concern in insulation, but some are still better than others. See below for the best blown and batt options.
- Avoid products with formaldehyde-based binders and those with flame retardant facing materials. Formaldehyde is a carcinogen and respiratory hazard, even at low levels. When formaldehyde-based binders are used in products, formaldehyde can be released into communities during manufacturing,[3] and residual levels may be released from products during use. Facing materials like ASJ (all service jacket), FSK (foil-scrim kraft), and PSK (polypropylene-scrim-kraft) may contain halogenated flame retardants, which can be persistent, bioaccumulative toxicants.
- Use mechanical installation methods, such as fasteners, whenever possible to avoid unnecessary use of adhesives, which can add additional hazards.
Expanded cork is a preferred choice in insulation in terms of chemical content and hazards. Cork has a long history of serving as an insulator. Well before plastic insulations like polystyrene came to market, cork was used as an insulating material.[4] Present-day cork insulation is produced using granulated bark from the cork oak tree which is compressed with steam until the granules swell and hold together to form slabs. Cork does not require flame retardants or other additives. It is expensive and may not be widely available, requiring advanced planning to allow for its use.
Blown wood fiber insulation may be installed as loose-fill insulation, in places like attics, or can be densely packed in places like wall cavities. It is made primarily of wood fibers. Flame retardants based on ammonium salts are commonly added but are believed to be low hazard.[5]
Within this type watch out for: Products using borate-based flame retardants. Boric acid, borax, and other borates are reproductive toxicants. Products that use these types of flame retardants are less preferred.
Insulation based on sheep’s wool can be in either blown-in or batt form. In both cases, the main component is sheep’s wool itself, accounting for more than 90% of the product. These products also commonly contain boric acid-based chemicals as a flame retardant and insect repellent.[6] Boric acid, borax, and other borates are reproductive toxicants.
Within this type prefer: Products that are mechanical needle punched and do not include a binder.
Within this type watch out for: Products with petrochemical binders like polyester. These will have greater impacts on fenceline communities during manufacturing.
Hemp fiber batts are made by combining together natural hemp fibers with a binder, commonly polyester fiber, and often a flame retardant.[7] While the majority of the product is natural (around ninety percent), the binders are commonly petroleum-based which can contribute to negative impacts on fenceline communities. Flame retardants used are typically low hazard.
Within this type prefer: Products that use plant-based binder materials or recycled binding fibers like recycled polyester, if the recycled content is of known origin and avoids hazardous content.
Within this type watch out for: Products using borate-based flame retardants. Boric acid, borax, and other borates are reproductive toxicants. Products that use these types of flame retardants are less preferred.
Wood fiber insulation is manufactured from waste wood chips and shavings that are generated during the manufacture of timber products. The insulation can either be rigid insulation boards or flexible insulation batts. Flexible batts are lighter and thicker than board insulation and are intended for interior use. In addition to the wood fibers themselves, the batts commonly include a flame retardant and polymer binder. The binders are commonly petroleum-based so can contribute to negative impacts on fenceline communities. Flame retardants used are typically low hazard.
Wood fiberboard insulation has been available for decades in Europe but is an emerging market in the United States. It can be made using either a wet or dry process. Wet process boards are typically denser and have a higher thermal conductivity (lower R-value) than dry process boards. They are more permeable to moisture, thus they are more suitable for indoor applications. Products manufactured using the dry process can be used in external walls and roofing applications. Binders are commonly based on isocyanates—asthmagens that are a concern during manufacturing.
Within this type watch out for: Products using borate-based flame retardants. Boric acid, borax, and other borates are reproductive toxicants. Products that use these types of flame retardants are less preferred.
Blown-in fiberglass or mineral wool insulation may be installed as:
- Loose-fill: usually used in attic applications where space is not limited.
- Dense-pack: more densely packed for wall cavities to prevent settling. (Dense-pack has the advantage that it can be used to upgrade the insulation of enclosed wall cavities).
- Spray-applied: usually with a small quantity of adhesive to adhere the insulation to the cavity.
Blown-in fiberglass and mineral wool insulations are made from individual strands of glass or mineral fibers.[8] These products commonly contain a small quantity of carcinogenic dedusting oils, used to keep dust levels down during manufacture and installation.
Within this type watch out for: Products that include a binder.[9] While not common, some of these products may include a binder which may have additional hazards throughout the product life cycle. Products that do not use a binder are often called “unbonded.”
Fiberglass batt insulation is made by combining fiberglass strands,[8] a dedusting oil like that used in loose fill insulation, and adding a binder to form batts. As of 2015 all four major manufacturers of residential fiberglass batt insulation in the US and Canada now use a formaldehyde-free binder. Small quantities of carcinogenic dedusting oils are commonly used.
Fiberglass batts come with several facing options that may add additional hazards. Unfaced batts are preferred.
Within this type prefer: Products that use a safer dedusting oil, like vegetable oil.
Within this type watch out for: Facers which will impact the color ranking due to additional hazardous content. Kraft-faced fiberglass batts are ranked yellow and PSK- or FSK-faced batts are ranked orange.
See Residential Fiberglass Insulation Transformed: Formaldehyde Is No More
Mineral wool is made from a molten mixture of rock and blast furnace slag from the steel industry.[8] The batt and semi-rigid board insulation is commonly still made using formaldehyde-based binders, but some products that use alternative, formaldehyde-free binders are now available.[10] Most typically, these products are unfaced.
Within this type watch out for: Formaldehyde-containing mineral wool batts and boards, which are orange in this Product Guidance. You can usually identify formaldehyde-free mineral wool products based on product names or descriptions in product literature such as transparency documents. In addition, this ranking is based on unfaced mineral wool batts. Facers may add additional hazards not reflected in this ranking.
Blown cellulose insulation is made using recycled newspapers, paperboard, or cardboard. The use of recycled materials cuts down on impacts associated with generating new materials. As a result, cellulose is expected to have fewer chemical impacts in manufacturing compared with many other insulation materials. However, it is not without impacts. Recycled paper and cardboard can include contaminant chemicals of concern such as bisphenols and orthophthalates. In addition, boric acid is commonly added as a flame retardant at around 15 percent of the product, by weight. While less of a concern than some other flame retardants common in insulation, boric acid is a reproductive toxicant. This can be a concern for occupants should dust make its way into living spaces.
Loose fill cellulose uses less insulation for a given R-value compared to dense pack or wet-applied, so uses a lower amount of boric acid, which is why it is ranked slightly better.
Fiberglass board insulation is made primarily from glass fibers[8] and a binder, with a small percentage of dedusting oil. Some products also include a facer. Facers often include halogenated flame retardants, which are commonly persistent, bioaccumulative toxicants, and a high priority to avoid. In addition, most fiberglass boards use a binder based on formaldehyde, but some formaldehyde-free products are now available. Unfaced formaldehyde-free fiberglass boards are a relatively low impact option for board insulation.
Within this type watch out for: Formaldehyde-containing fiberglass boards, which are orange in this Product Guidance. You can usually identify formaldehyde-free products based on descriptions in product literature such as transparency documents. In addition, this ranking is based on unfaced boards. Facers may add additional hazards. ASJ- or FSK-faced fiberglass boards are ranked red.
Fiberglass batt insulation is made by combining fiberglass strands,[8] a dedusting oil like that used in loose fill insulation, and adding a binder to form batts. As of 2015 all four major manufacturers of residential fiberglass batt insulation in the US and Canada now use a formaldehyde-free binder.
Fiberglass batts come with several facing options including kraft paper, foil, or a polyethylene film. Paper is the most affordable and most popular facing option and has an asphalt-impregnated paper facer that acts as a vapor retarder. Asphalt is considered a carcinogen and can impact workers and communities near manufacturing sites. Use unfaced batts whenever possible. Like unfaced batts, kraft-faced batts commonly include a small percentage of a carcinogenic dedusting oil.
Within this type prefer: Products that use a safer dedusting oil, like vegetable oil.
Batt insulation made from recycled cotton, cellulose, or a blend of the two contains about 7% boric acid as a flame retardant. Boric acid is a reproductive toxicant which may be a concern, particularly during installation or if dust enters the living space. Government agencies have raised fewer human health concerns about boric acid than for other flame retardants—particularly halogenated flame retardants, which can be persistent and bioaccumulative.
The use of recycled materials cuts down on impacts associated with generating new materials. As a result, insulation using recycled cellulose and cotton is expected to have fewer chemical impacts in manufacturing compared with many other insulation materials. However, cellulose and cotton batts do contain around 9% of a binder like polyester fibers, which is petroleum-based.
Most typically, these products are unfaced. Facers may add additional hazards not reflected in this ranking.
Within this type prefer: Products that use ammonium phosphate salt rather than boric acid as a flame retardant.
Blown cellulose insulation is made using recycled newspapers, paperboard, or cardboard. The use of recycled materials cuts down on impacts associated with generating new materials. As a result, cellulose is expected to have fewer chemical impacts in manufacturing compared with many other insulation materials. However, it is not without impacts. Recycled paper and cardboard can include contaminant chemicals of concern such as bisphenols and orthophthalates. In addition, boric acid is commonly added as a flame retardant at around 15 percent of the product, by weight. While less of a concern than some other flame retardants common in insulation, boric acid is a reproductive toxicant. This can be a concern for occupants should dust make its way into living spaces.
Dense pack and wet-blown cellulose insulation uses a larger quantity of insulation for a given R-value which results in a higher amount of boric acid compared to loose fill cellulose. This is why it is ranked slightly worse.
Some fiberglass batts or blankets are faced with flame retardant facers, such as PSK (polypropylene-scrim-kraft) and FSK (foil-scrim-kraft). Like kraft-faced fiberglass batts, these products commonly rely on a carcinogenic dedusting oil and asphalt-based adhesive. Additionally, the facers may include halogenated flame retardants. These chemicals are a high priority to avoid because they can be persistent, bioaccumulative, and toxic. Use unfaced batts or other products that are ranked in the green when possible.
Within this type prefer: Products that use a safer dedusting oil, like vegetable oil or sunflower seed oil. In addition, prefer unfaced products ranked light green in this guidance.
Within this type watch out for: Products using formaldehyde-based binders. In particular, some duct wrap products may still use formaldehyde-based binders. You can usually identify formaldehyde-free fiberglass duct wrap insulation based on product names or descriptions in product literature (such as transparency documents).
It is not clear whether products without halogenated flame retardants are available. If you must use batts or blankets with a flame retardant facer, ask manufacturers for products that don’t contain these priority chemicals.
Mineral wool is made from a molten mixture of rock and blast furnace slag from the steel industry.[8] The fibers are commonly sprayed with a formaldehyde-based binder and formed into batts or boards before being put through an oven to cure. Most typically, these products are unfaced, and this ranking is based on unfaced mineral wool batts and boards. Facers may add additional hazards not reflected in this ranking.
Formaldehyde, a carcinogen and asthmagen, can be released into communities during manufacturing. Small quantities of residual formaldehyde can also be released into living spaces during use. Some mineral fiber batt and board insulation has become available without formaldehyde-based binders.
Within this type prefer: Products that are formaldehyde-free (ranked light green in this guidance).
Fiberglass board insulation is made of the fibers[8] and typically a formaldehyde-based binder. Formaldehyde, a carcinogen and asthmagen, can be released into communities during manufacturing. Small quantities of residual formaldehyde can also be released into living spaces during use.
Fiberglass board insulation made with a formaldehyde-free binder is beginning to enter the market.
Within this type prefer: Products that are formaldehyde-free, which are light green in this guidance. You can usually identify formaldehyde-free products based on descriptions in product literature such as transparency documents.
Within this type watch out for: Facers on fiberglass board insulation. This ranking is based on unfaced fiberglass boards. Facers may add additional hazards, for example, ASJ or FSK-faced fiberglass boards are ranked red in this guidance.
Polyisocyanurate (polyiso) board consists of a foam core made by reacting isocyanates and polyols. This core is sandwiched between aluminum and kraft paper facers or fiberglass mat. Most polyiso boards contain TCPP, a chlorinated flame retardant which is part of the larger chemical group of halogenated flame retardants. Halogenated flame retardants are considered a very high concern to avoid because they can be persistent and toxic. Halogen-free polyiso products are a better option because they avoid halogenated flame retardants, instead using a non-halogenated reactive flame retardant that becomes part of the polyiso polymer. This means that the flame retardant is less likely to be released from the product into buildings. The reactive flame retardant is also assessed to be of relatively lower hazard than halogenated flame retardants even before reacting.[11]
Isocyanates, used in the production of polyisocyanurate, are a leading cause of work-related asthma and also use polluting chemistry in their manufacture.[12]
Within this type watch out for: Standard polyiso products, which include halogenated flame retardants and are ranked red in this guidance. Halogen-free polyiso can usually be identified by an “NH” in the product name.
Fiberglass board insulation is made of glass fibers[8] and typically a formaldehyde-based binder. Formaldehyde (a carcinogen and asthmagen) can be released into communities during manufacturing. Small quantities of residual formaldehyde can also be released into living spaces during use. Fiberglass board insulation made with a formaldehyde-free binder is beginning to enter the market. Use these products whenever possible or select other product types ranked better in this guidance.
Fiberglass boards faced with flame retardant facers, such as ASJ (all service jacket) and FSK (foil-scrim-kraft), may include halogenated flame retardants. These chemicals are a high priority to avoid because they can be persistent, bioaccumulative, and toxic.
Within this type prefer: Products that are unfaced and formaldehyde-free, which are light green in this guidance. You can usually identify formaldehyde-free products based on descriptions in product literature such as transparency documents.
It is not clear whether products without halogenated flame retardants are available. If you must use boards with a flame retardant facer, ask manufacturers for products that don’t contain these priority chemicals.
Expanded polystyrene insulation is made by expanding individual pre-formed beads of polystyrene into a molded shape, similar to how polystyrene coffee cups are made. EPS insulation has historically contained the flame retardant hexabromocyclododecane (HBCD) which is highly toxic, persistent in the environment, and bioaccumulative. According to the industry association, their members, who account for an estimated 80-85% of the EPS insulation manufactured in the United States, stopped using HBCD by 2017. It is not clear whether any of the remaining portion of EPS still contains HBCD, but the US EPA is in the process of proposing regulation around the use of HBCD.[13]
The common replacement flame retardant is still halogenated like HBCD and presents life cycle concerns, including the potential for hazardous breakdown products.[14]
Within this type watch out for: Some specialty EPS insulation that contains an insecticide to make it resistant to termites which might otherwise burrow into it when used below grade. A commonly used insecticide is known to be hazardous to bees and is a potential endocrine disruptor.[15] Avoid these products.
Polyisocyanurate board consists of a foam core made by reacting isocyanates and polyols. This core is sandwiched between aluminum and kraft paper facers or fiberglass mat. Polyisocyanurate boards typically contain TCPP, a halogenated flame retardant. Halogenated flame retardants are considered a very high concern to avoid because they can be persistent and toxic.
Within this type prefer: Products that are halogen-free, which are ranked orange in this guidance. Halogen-free polyiso can usually be identified by an “NH” in the product name. The better ranked polyiso is still in the orange, so try to use different types of products that are ranked green or yellow.
Extruded polystyrene is made from similar polystyrene beads as EPS, but the beads are extruded into a solid block. The result is that there are fewer pores between the beads which makes XPS an air barrier. XPS has historically contained the flame retardant hexabromocyclododecane (HBCD) which is persistent, bioaccumulative, and toxic. The major manufacturers of XPS indicate they have transitioned away from the use of HBCD. Unfortunately, the common replacement flame retardant is still halogenated like HBCD. The health hazards of this alternative have not been fully studied and it presents life cycle concerns, including the potential for hazardous breakdown products.[14]
XPS also relies on a halogenated blowing agent. Until recently, hydrofluorocarbons (HFCs) were the most commonly used and contribute to global warming. As much as 10% of the weight of the board is this blowing agent, which is 1,430 times more potent than carbon dioxide at warming the planet.[16] Regulations in several states in the US have prompted some manufacturers to transition away from HFCs, instead using hydrofluoroolefins (HFOs).[17] While HFOs do not themselves have high GWP, they do use high GWP and/or ozone depleting substances in the manufacturing process which can still be released into the environment. Some halogenated blowing agents are also members of the class of chemicals called PFAS or “forever chemicals.”
See Beware the Hidden Ozone Depleter: Upstream Impacts of Blowing Agents.
Spray polyurethane foam insulation is sold as a two-part liquid that is then combined and applied on-site. Part A is a mixture of isocyanates, and Part B is a mixture of polyols and other additives. This reaction produces polyurethane, and releases small amounts of isocyanates and other chemicals into the surrounding area, which can expose installers and others in the vicinity to these hazardous ingredients. Excessive heat release can also lead to fires in extreme cases. Offgassing from SPF can occur for extended periods after installation.[18]
Isocyanates are asthmagens and have been identified as a leading cause of work-related asthma by organizations like the US Occupational Safety and Health Administration (OSHA).[19] Part B of the foam mixture includes a halogenated flame retardant. Halogenated flame retardants are considered a very high concern to avoid because they can be persistent and toxic.
Closed cell spray foam also commonly uses a halogenated blowing agent, a hydrofluorocarbon (HFC), that is a highly potent contributor to global warming. Regulations in several states in the US have prompted some manufacturers to transition away from HFCs, instead using hydrofluoroolefins (HFOs).[20] While HFOs do not themselves have high GWP, they do use high GWP and/or ozone depleting substances in the manufacturing process which can still be released into the environment. Some halogenated blowing agents are also members of the class of chemicals called PFAS or “forever chemicals.”
See Careful Insulation Selection and Installation Can Protect R-Value and Health and Beware the Hidden Ozone Depleter: Upstream Impacts of Blowing Agents.
Supporting Information
Unless otherwise noted, product content and health hazard information is based on research done by Habitable for Common Product profiles, reports, and blogs. Links to the appropriate resources are provided.
Common Product Records Sourced
- ASJ-Faced Fiberglass Board Insulation
- Blown-in Cellulose Insulation
- Closed Cell Spray Foam Insulation
- EPS Insulation (expanded polystyrene)
- Expanded Cork Board Insulation
- FSK-faced Fiberglass Duct Wrap
- Historical: EPS Insulation (expanded polystyrene) - 2015
- Historical: XPS Insulation (extruded polystyrene) - 2015
- Kraft-faced Fiberglass Batt Insulation
- Mineral Fiber Batt Insulation
- Mineral Wool Board Insulation
- Polyisocyanurate Wall Insulation Board
- Post-Consumer Newsprint
- Post-Consumer Paperboard
- Spray-applied Fiberglass Insulation
- Unbonded Blown-in Fiberglass Insulation
- Unfaced Cellulose/Cotton Batt Insulation
- Unfaced Fiberglass Batt Insulation
- Wet-Blown Cellulose Insulation
- Wood Fiber Insulation Boards
- XPS Insulation (extruded polystyrene)
Endnotes
[1] “Environmental Impacts of Natural Gas,” Union of Concerned Scientists, June 19, 2014, https://www.ucsusa.org/resources/environmental-impacts-natural-gas.; Tim Donaghy and Charlie Jiang, “Fossil Fuel Racism: How Phasing Out Oil, Gas, and Coal Can Protect Communities,” April 13, 2021, https://www.greenpeace.org/usa/reports/fossil-fuel-racism/.
[2] “Making Affordable Multifamily Housing More Energy Efficient: A Guide to Healthier Upgrade Materials.” Energy Efficiency for All, September 2018. https://informed.habitablefuture.org/resources/research/11-making-affordable-multifamily-housing-more-energy-efficient-a-guide-to-healthier-upgrade-materials.
[3] Vallette, James. “Residential Fiberglass Insulation Transformed: Formaldehyde Is No More.” Healthy Building Network, October 30, 2015. https://informed.habitablefuture.org/resources/news/131-residential-fiberglass-insulation-transformed-formaldehyde-is-no-more.
[4] Bozsaky, Dávid. “The Historical Development of Thermal Materials.” Periodica Polytechnica Architecture 41, no. 2 (n.d.): 49–56. https://doi.org/10.3311/pp.ar.2010-2.02.
[5] Schneider. “Technical Datasheet: Best Wood Fibre,” September 2022. https://www.schneider-holz.com/en/service/downloads/download/technical-data-sheet-fibre/.; TimberHP. “Product Data Sheet: TimberFill,” August 2022. https://timberhpassets.s3.amazonaws.com/wp-content/uploads/2022/08/03223339/22_0803_TimberHP_Cut_Sheets_TimberFill.pdf.; Gutex. “Thermofibre Data Sheet,” December 2020. https://gutex.de/fileadmin/uploads/Downloads/Technische_Merkblaetter/GUTEX_EN_TD_Thermofibre_2020-12.pdf.; Steico. “STEICOzell.” Accessed October 27, 2022. https://www.steico.com/en/products/insulation/insulation-between-studs/air-injected-insulation/steicozell.
[6] Havelock Wool. “Health Product Declaration: Havelock Wool Insulation,” January 2, 2020. https://hpdrepository.hpd-collaborative.org/repository/HPDs/publish_672_Havelock_Wool_Insulation.pdf.; Havelock Wool. “Our Products.” Accessed December 20, 2022. https://havelockwool.com/residential-insulation/.; Wool Life. “Natural Wool Insulation.” Accessed December 20, 2022. https://naturalwool-insulation.com/natural-wool-insulation-in-the-usa/.; Lehner Wool. “ISOLENA Insulation.” Accessed December 20, 2022. https://www.lehner-wool.com/en/brands/isolena.html.; Havelock Wool. “Havelock Wool Batt and Loose-Fill Insulation LCA Results & Interpretation,” June 5, 2020. https://transparencycatalog.com/company/havelock-wool-insulation/showroom/havelock-wool-insulation/lca-results.;Eden Renewable Innovations Limited. “Environmental Product Declaration: Thermafleece Cosywool, Ultrawool,” November 1, 2021. https://www.thermafleece.com/uploads/pro_20211201123642.pdf.
[7] Nature Fibres, Inc. “Health Product Declaration: Natur-Chanv/Hemp Hemp Fiber Batt Insulation,” June 30, 2021. https://hpdrepository.hpd-collaborative.org/repository/HPDs/1012_Natur_Chanv_Hemp_Hemp_Fiber_Batt_Insulation.pdf.; Hempitecture. “Technical Data: HempWool,” 2022. https://cdn.shopify.com/s/files/1/0314/7137/0377/files/HempWool_TDS_2022.1.pdf?v=1661729297.; Hempitecture. “HempWool Frequently Asked Questions.” Accessed December 20, 2022. https://www.hempitecture.com/faq.; Ekolution AB. “Environmental Product Declaration: Ekolution Hemp Fibre Insulation,” October 9, 2020. https://api.environdec.com/api/v1/EPDLibrary/Files/b1030640-bd7d-46f0-9bce-b4ce6335b672/Data.; Hemspan. “Bio Wall Hemp Insulation Technical Specifications,” July 2022. https://hemspan.com/wp-content/uploads/2022/07/Bio-Wall-Tech-Specs-2022-.pdf.; Atteberry, Wade. Hemp insulation fire retardant applicator and method. United States US20220266076A1, filed February 24, 2021, and issued August 25, 2022. https://patents.google.com/patent/US20220266076A1/en.; Gleich, Anmelder. Flame, fire and glow-protected natural fiber insulation materials and their production and use, in particular for natural fiber insulation products. Germany DE102019107982A1, filed March 28, 2019, and issued October 1, 2020. https://patents.google.com/patent/DE102019107982A1/en.; Piechatzek, Guenter Alois. Insulation mat based on hemp fibers and process and equipment for their production. Germany DE10148376B4, filed September 29, 2001, and issued June 22, 2006. https://patents.google.com/patent/DE10148376B4/en.; Eden Renewable Innovations Limited. “Material Safety Data Sheet: Thermafleece Hemp,” January 3, 2012. https://www.celticsustainables.co.uk/content/Hemp/Thermafleece%20Hemp%20MSDS.pdf.; Nature Fibres, Inc. “Health Product Declaration: Natur-Bois/Wood Hemp-Wood Fiber Batt Insulation,” June 30, 2021. https://hpdrepository.hpd-collaborative.org/repository/HPDs/1012_Natur_Bois_Wood_Hemp_Wood_Fiber_Batt_Insulation.pdf.
[8] Respirable dusts and fibers can pose an inhalation hazard for workers. The level of hazard depends on the shape, size, and durability of the dusts and fibers. While some specialty glass fibers are carcinogens, the glass and mineral fibers used in fiberglass and mineral wool insulation are not currently classified as carcinogens because they are biosoluble (readily dissolved and cleared from the lungs). In 1988, the International Agency for Research on Cancer (IARC) released a monograph on man-made mineral fibers. This study concluded that mineral wool fibers (including glass and rock or slag wool) were “possibly carcinogenic to humans.” In 2002, new data from additional studies were reviewed and incorporated into a new monograph that concluded that the type of mineral wool fibers used in insulation are, “not classifiable as to their carcinogenicity to humans.” In 2011, both the National Toxicology Program (NTP) and the California Office of Environmental Health Hazard Assessment (OEHHA) made a distinction in their listings between biosoluble glass and mineral fibers, which are cleared from the body, and certain other glass or mineral fibers that are inhalable and persist in the body (are biopersistent). This change meant that the cancer hazard association and a cancer warning, which was previously required on packaging, were no longer warranted for products using biosoluble fibers. The prior labeling of fiberglass insulation products with cancer warnings has led to some confusion in the industry, but the scientific consensus is that the biosoluble glass fibers that are used in insulation are not classified as carcinogens. Glass fibers from insulation can cause temporary eye, skin, and lung irritation. As with all products, proper personal protective equipment (PPE) should be used for installation or removal of products.
See: “IARC Monographs on the Evaluation of Carcinogenic Risks to Humans: Volume 81 Man-Made Vitreous Fibers.” World Health Organization: International Agency for Research on Cancer, 2002. http://monographs.iarc.fr/ENG/Monographs/vol81/mono81.pdf.; “IARC Monographs on the Evaluation of Carcinogenic Risks to Humans: Volume 43 Man-Made Mineral Fibers and Radon.” World Health Organization: International Agency for Research on Cancer, 1998. http://monographs.iarc.fr/ENG/Monographs/vol43/mono43.pdf.; “Modification of the Listing of Glasswool Fibers (Airborne Particles of Respirable Size) to Glass Wool Fibers (Inhalable and Biopersistent).” OEHHA, November 18, 2011. https://oehha.ca.gov/proposition-65/crnr/modification-listing-glasswool-fibers-airborne-particles-respirable-size-glass.; “New Substances Added to HHS Report on Carcinogens.” NIEHS, June 10, 2011. https://web.archive.org/web/20110817141807/http://www.niehs.nih.gov:80/news/releases/2011/roc/.; “ToxFAQsTM for Synthetic Vitreous Fibers.” Toxic Substances Portal - Agency for Toxic Substances & Disease Registry. Accessed June 14, 2017. https://www.atsdr.cdc.gov/toxfaqs/tf.asp?id=907&tid=185.
[9] Rockwool Nordics. “Environmental Product Declaration: Rockwool Granulate Thermal Insulation for the Nordics Market,” March 24, 2022. https://www.epd-norge.no/getfile.php/1323185-1648576959/EPDer/Byggevarer/Isolasjon/NEPD-3410-2023_ROCKWOOL----Granulate-thermal-insulation-for-the-Nordics-market-.pdf.
[10] “Formaldehyde-Free Thermafiber® Mineral Wool Insulation.” Owens Corning. Accessed December 20, 2022. https://www.owenscorning.com/formaldehyde-free.; “AFB Evo Technical Data Sheet.” Rockwool, January 1, 2018. https://cdn01.rockwool.com/siteassets/o2-rockwool/documentation/technical-data-sheets/commercial/AFB-evo-Formaldehyde-Free-Techdata.pdf?f=20181016101455.
[11] “EnergyGuard NH Polyiso Insulation Health Product Declaration.” GAF, March 15, 2018. https://hpdrepository.hpd-collaborative.org/repository/HPDs/publish_112_EnergyGuard_NH_Polyiso_Insulation_1521152481.pdf; Nandi, Malay, Lance Wang, and Jawed Asrar. Roofing systems and roofing boards with non-halogenated fire retardant. World Intellectual Property Organization WO2015191392A1, filed June 5, 2015, and issued December 17, 2015. https://patents.google.com/patent/WO2015191392A1/en.
[12] US EPA, OCSPP. “Potential Chemical Exposures From Spray Polyurethane Foam.” Overviews and Factsheets. Accessed March 30, 2017. https://www.epa.gov/saferchoice/potential-chemical-exposures-spray-polyurethane-foam; Vallette, Jim. “Chlorine and Building Materials: A Global Inventory of Production Technologies, Markets, and Pollution - Phase 1: Africa, The Americas, and Europe.” Healthy Building Network, July 2018.https://habitablefuture.org/resources/chlorine-building-materials-project-phase-1-africa-the-americas-and-europe/.
[13] US EPA. “Final Risk Evaluation for Cyclic Aliphatic Bromide Cluster (HBCD).” Accessed December 20, 2022. https://www.epa.gov/assessing-and-managing-chemicals-under-tsca/final-risk-evaluation-cyclic-aliphatic-bromide-cluster.
[14] Bienkowski, Brian. “‘Environmentally Friendly’ Flame Retardants Break down into Potentially Toxic Chemicals.” Environmental Health News, January 9, 2019. https://www.ehn.org/environmentally-friendly-flame-retardants-break-down-into-potentially-toxic-chemicals-2625440344.html.; Minet, Laura, Arlene Blum, Seth R. Fernández, Kathryn M. Rodgers, Veena Singla, Anna Soehl, and Miriam L. Diamond. “High Production, Low Information: We Need To Know More About Polymeric Flame Retardants.” Environmental Science & Technology, February 22, 2021. https://doi.org/10.1021/acs.est.0c08126.
[15] Imidacloprid is listed in the All Contents of the Common Product profile. Hazards to bees are documented in, for example: Dively, G. P., et. al. (2014). "Assessment of chronic sublethal effects of imidacloprid on honey bee colony health." PloS one, 10(3), e0118748-e0118748. http://journals.plos.org/plosone/article?id=10.1371/journal.pone.0118748; EPA. "Pesticide News Story: EPA Issues Registration Review Final Work Plan for Imidacloprid." Press release, July 13, 2009. http://www.epa.gov/oppfead1/cb/csb_page/updates/2009/imidacloprid.html; Darriet, F., & Chandre, F. (2013). "Efficacy of six neonicotinoid insecticides alone and in combination with deltamethrin and piperonyl butoxide against pyrethroid‐resistant Aedes aegypti and Anopheles gambiae (Diptera: Culicidae)." Pest management science, 69(8), 905-910. http://www.ncbi.nlm.nih.gov/pubmed/23208775; Dai, P. L., et. al. (2010). "Effects of sublethal concentrations of bifenthrin and deltamethrin on fecundity, growth, and development of the honeybee Apis mellifera ligustica." Environmental Toxicology and Chemistry, 29(3), 644-649. http://www.ncbi.nlm.nih.gov/pubmed/20821489; Cohnstaedt, L. W., & Allan, S. A. (2011). "Effects of sublethal pyrethroid exposure on the host‐seeking behavior of female mosquitoes." Journal of Vector Ecology, 36(2), 395-403. http://naldc.nal.usda.gov/download/55704/PDF. Imidacloprid is also listed as a potential endocrine disruptor by TEDX: https://endocrinedisruption.org/interactive-tools/tedx-list-of-potential-endocrine-disruptors/search-the-tedx-list.
[16] US EPA, “Global Warming Potentials and Ozone Depletion Potentials of Some Ozone-Depleting Substances and Alternatives Listed by the SNAP Program,” last updated November 6, 2014, http://www3.epa.gov/ozone/snap/subsgwps.html
[17] Bettenhausen, Craig. “Rigid Foam Insulation Gets a Climate Chemistry Upgrade.” Chemical & Engineering News, May 25, 2021. https://cen.acs.org/environment/greenhouse-gases/Rigid-foam-insulation-climate-chemistry/99/i20.
[18] A microchamber emission study published by the National Institute of Standards and Technology (NIST) concluded that, “emissions from SPF can be highly variable.” TCPP, the common chlorinated flame retardant used, was detected in emissions from all four samples tested, including one that was tested 18 months after application. Other chemicals were found to be emitted as well. One sample, taken from a residential application of closed-cell SPF (applied during the summer of 2015 and tested March 2016), emitted more than 80 different chemicals. As the study’s authors note, these chemicals may not all have negative health impacts, but some most likely do, including the carcinogens 1,4-dioxane and 1,2-dichloropropane. See: Poppendieck, Dustin G., Mengyan Gong, and Lauren E. Lawson. “Lessons Learned from Spray Polyurethane Foam Emission Testing Using Micro-Chambers.” In The 59th Annual Polyurethanes Technical Conference. Baltimore, MD, 2016. http://ws680.nist.gov/publication/get_pdf.cfm?pub_id=921259.
See also: US Environmental Protection Agency. “Vacate and Safe Re-Entry Time for Spray Polyurethane Foam Application.” Overviews and Factsheets. Accessed March 7, 2017. https://web.archive.org/web/20200810001246/https://www.epa.gov/saferchoice/vacate-and-safe-re-entry-time-spray-polyurethane-foam-application.
[19] US Occupational Safety and Health Administration, “OSHA Fact Sheet: Do You Have Work-Related Asthma? A Guide for You and Your Doctor,” March 2014, https://www.osha.gov/Publications/OSHA3707.pdf; Kenneth D. Rosenman, Mary Jo Reilly, and Barton G. Pickelman, “2019 Annual Report Tracking Work-Related Asthma in Michigan” (Michigan State University, July 20, 2020), https://oem.msu.edu/images/annual_reports/2019-WRA-Annual-Report-FINAL.pdf; Daniel Lefkowitz et al., “Isocyanates and Work-Related Asthma: Findings from California, Massachusetts, Michigan and New Jersey, 1993-2008,” American Journal of Industrial Medicine 58, no. 11 (November 2015): 1138–49, https://doi.org/10.1002/ajim.22527; While reported incidences have declined in recent years, limited data are available to gauge the scope of the issue.
[20] Bettenhausen, Craig. “Rigid Foam Insulation Gets a Climate Chemistry Upgrade.” Chemical & Engineering News, May 25, 2021. https://cen.acs.org/environment/greenhouse-gases/Rigid-foam-insulation-climate-chemistry/99/i20.
Last updated: January 5, 2023