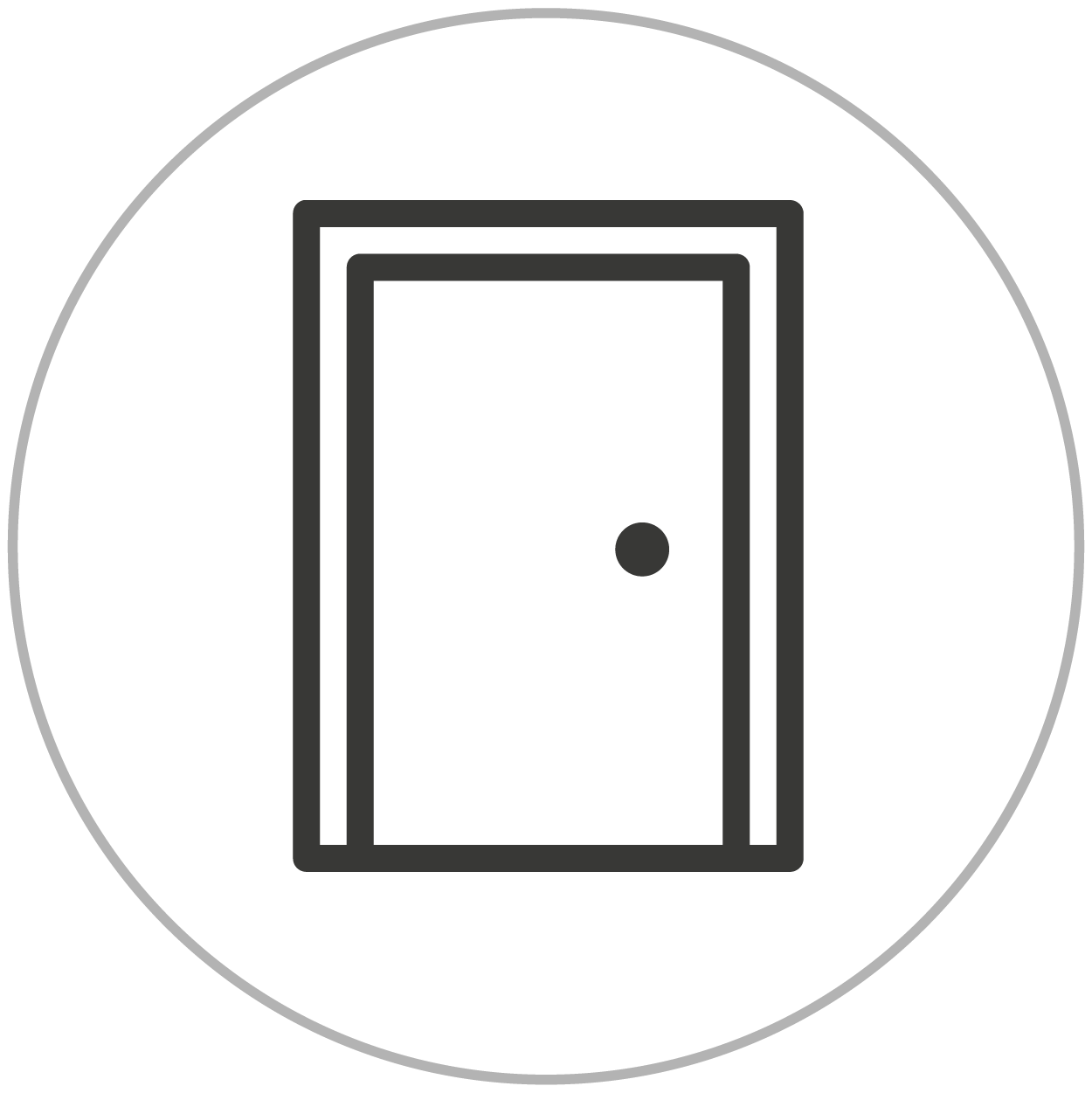
Interior Wood Doors, Cabinetry, and Millwork Product Guidance
Use the red-to-green product guidance below to select safer product types by avoiding those in red and preferring yellow and green, which are safer for occupants, fenceline communities, and workers.
When choosing interior wood doors, cabinetry, and millwork:
- Prefer solid wood materials over composite.
- Opt for plywood over other composite wood whenever possible.
- When using composite wood, specify materials that are NAF (No Added Formaldehyde) whenever possible.
- Prefer solid wood veneer facings over laminate, melamine, or thermofoil.
- Prefer solid wood veneer edge banding over plastics like melamine and PVC.
- If staining or painting is necessary, prefer water-based factory-applied finishes.
- Avoid adhesives when possible and prefer mechanical joining methods.
- Avoid hardware that contains antimicrobial treatments.
Composite wood products are widely used for applications such as countertop substrates and in cabinetry, doors, and millwork. These products are made from wood particles, fibers, and/or plies that are held together with adhesives known as ‘binders.’ Binders can have impacts on human health during the manufacturing process, exposing workers and nearby communities, and during product use. Driving factors for the material health rankings below are: 1) the type of binder and associated hazards during manufacturing and use, 2) the quantity of binder material in the product type (because of the life cycle impacts of petrochemicals), and 3) the length of life of the material (products that last longer can be replaced less frequently, reducing the chemical impacts over a building’s life).
Binders are commonly based on formaldehyde (a carcinogen and asthmagen) which can be emitted from composite wood products over time.[1] Because of this, interior composite wood products are regulated. A number of different terms and acronyms, regulatory and not, are applied to composite wood which can make specifying these products confusing. Here is a breakdown of the most common acronyms and what they mean:
- CARB Phase 2 or TSCA Title VI Compliant. This means that the composite wood product meets the minimum regulatory requirements set by the California Air Resources Board (CARB) or the federal regulatory requirements set by the U.S. EPA under the Toxic Substances Control Act (TSCA). While there are minor differences between the California and federal regulations, the formaldehyde emissions limits for composite wood products are identical.[2] All interior plywood, MDF, and particleboard sold in the United States must meet one of these two regulatory standards.
- ULEF (Ultra Low Emitting Formaldehyde). This is a regulatory term that describes composite wood containing formaldehyde-based binders that has been shown to consistently have lower formaldehyde emissions than the regulatory requirements in a controlled laboratory setting.[3]
- NAF (No Added Formaldehyde). This is a regulatory term that describes composite wood that does not contain binders made with formaldehyde. The most common formaldehyde alternatives are based on isocyanates or a combination of soy flour and synthetic polymers.
- NAUF (No Added Urea Formaldehyde). This is not a regulatory term, but composite wood manufacturers sometimes use it to differentiate products that use formaldehyde-based binders that are not based on urea formaldehyde. All products containing formaldehyde-based binders have small amounts of formaldehyde that can be released over time, but urea formaldehyde can undergo a chemical reaction when exposed to moisture that releases additional formaldehyde.[4] Because of this, some building standards have had requirements to avoid urea formaldehyde. NAUF is not equivalent to any of the regulatory terms listed above.
Testing on regulated products is only conducted on the composite wood material, not on the finished goods such as door and cabinet assemblies.[5] Some adhesives used to assemble finished goods can contain formaldehyde and other hazardous chemicals, and these are not considered by the regulations.
Another important consideration is that formaldehyde emission testing is performed at set conditions (25 ± 1°C and 50 ± 4% relative humidity),[6] but formaldehyde emissions are known to be higher at elevated temperatures and humidities.[7] This means that products which meet emission requirements could release formaldehyde at much higher levels when installed in a building without an air conditioner or with the air conditioner turned off during a hot and/or humid period.
The best way to avoid formaldehyde exposures throughout the product life cycle is to purchase products that do not contain formaldehyde-based binders or adhesives. This can be done by selecting composite wood products designated as NAF (No Added Formaldehyde), by using solid wood, and by avoiding formaldehyde based adhesives in assemblies. You can also reduce toxic exposures by selecting composites with the smallest amount of binder: plywood generally contains less binder than medium density fiberboard (MDF) and particleboard.
Note that both national (TSCA Title VI) and California-based (CARB) regulations that legally limit formaldehyde emissions in composite wood only apply to hardwood plywood, MDF, and particleboard. Low-density fiberboard (LDF) and high-density fiberboard (HDF) can also fall under the definition of MDF depending on how they are marketed and used, and are considered to be MDF in this guidance.[8] Other composite wood products including hardboard, structural plywood, oriented strand board (OSB), glue laminated timber, cross laminated timber, wood I-joists, and finger-jointed lumber, are exempted from these regulations.[9]
While products containing NAF binders may be better for installers and people occupying the spaces where the composite wood is installed, they are still produced using chemicals that can impact the health of workers across the supply chain and nearby communities. The two most common binders are based on isocyanates (the building blocks of polyurethanes) or a mixture of soy flour and synthetic resin. As with formaldehyde-based binders, both alternative binders contain chemicals derived from hazardous inputs. They also contain petrochemicals, which is a concern because living in close proximity to oil and gas wells has been associated with numerous health impacts, including adverse pregnancy outcomes, cancer, exacerbation of asthma, and mental health issues.[10] A recent body of research also demonstrates that oil and gas wells are disproportionately located near historically redlined communities composed of high percentages of people of color, contributing to environmental injustice.[11] As a result, wood that does not contain any synthetic binder is considered best in class.
Here is some additional, more detailed guidance to use when choosing interior wood doors, cabinetry, and millwork:
- Prefer solid wood materials over composite. All composite wood requires chemicals that can impact the health of workers and nearby communities during manufacturing and some of these chemicals can also impact the health of building occupants and installers.
- Opt for plywood over other composite wood whenever possible. Plywood generally contains lower amounts of binder than MDF and particleboard. Plywood products with an MDF or particleboard core or veneer are less preferred, but are slightly preferable to an MDF or particleboard product of equivalent thickness.
- When using composite wood, specify materials that are NAF (No Added Formaldehyde) whenever possible. While all plywood, MDF, and particleboard is required to meet formaldehyde emissions limits, specifying NAF ensures that chemicals containing formaldehyde are not added to the product at all.
- Prefer solid wood veneer facings over laminate, melamine, or thermofoil. Laminate and melamine facings are thin layers of paper impregnated with formaldehyde-based resins. Thermofoil is usually composed of polyvinyl chloride (also called PVC or vinyl). The manufacture of PVC requires the use of many hazardous chemicals that impact workers and nearby communities.[12] PVC also has end of life concerns including its potential to form persistent, bioaccumulative toxicant dioxins when burned.[13]
- Prefer solid wood veneer edge banding over plastics like melamine and PVC. Plastic edge banding materials have greater life cycle chemical impacts than solid wood veneers.
- If staining or painting is necessary, prefer water-based factory-applied finishes. Factory-applied finishes will limit exposures to a more controlled environment, but can still impact workers. Wood finishes can contain many harsh solvents that are hazardous and/or contribute to smog formation. Some finishes may contain or emit formaldehyde over time after manufacture - this is a known issue with acid-catalyzed or conversion varnishes. Formaldehyde-free varnishes are available. See our Interior Paint Product Guidance for considerations related to some other types of coatings that may be applied to doors, cabinetry, and millwork.
- Avoid adhesives when possible and prefer mechanical joining methods. Adhesives can add hazardous content. The best option is to avoid using adhesives when possible. When adhesives are necessary, prefer polyvinyl acetate adhesives, which have fewer concerns than adhesives based on formaldehyde.
- Avoid hardware that contains antimicrobial treatments. No evidence yet exists to demonstrate that products intended for use in interior spaces that incorporate antimicrobial additives actually result in healthier populations. Further, antimicrobials may have negative impacts on both people and the environment.[14]
Whenever feasible, solid wood is preferable to composite wood because it does not require binders or other additives.
Within this product type prefer: Pre-finished solid wood to keep stains and topcoat chemicals within a factory setting and off of the building site where workers and occupants are less protected.
As the name implies, no added formaldehyde (NAF) plywood contains a binder made without formaldehyde. There are two common types of NAF binders. The first is made from isocyanates and the second is made by combining soy flour with a synthetic resin. Both types of binder are of relatively low concern to building occupants and installers.[15]
Since both types of NAF binders are manufactured using a number of hazardous chemicals they can, however, impact workers and nearby communities. Isocyanates are potent respiratory sensitizers that are made using many hazardous chemicals, including several carcinogens.[16] The soy-based binder is made by reacting soy flour with a polyamide and epichlorohydrin resin.[17] Both the polyamide and epichlorohydrin resins use carcinogens and/or reproductive toxicants in their production.[18]
Plywood typically has a longer service life than medium density fiberboard and particleboard.[19] It also typically requires less binder, which means it requires lower levels of hazardous chemicals and lower levels of petrochemicals to manufacture than other products.
Standard plywood products contain binders based on formaldehyde, a carcinogen. Residual formaldehyde is gradually released from these products over time.[20] ULEF products have demonstrated that they consistently meet stricter formaldehyde emission limits than standard products at the conditions tested, so they are somewhat preferable to standard products. However, both can use urea formaldehyde binders, which react with moisture in the air and can release higher levels of formaldehyde than seen under the test conditions. They also use hazardous chemicals during manufacturing that can impact fenceline communities and workers. So, while ULEF plywood is better under some conditions during use, across its life cycle the impacts are similar to standard plywood. See the Read More section for more background on regulations and terminology.
Plywood typically has a longer service life than MDF and particleboard. It also typically requires less binder, which means it requires lower levels of hazardous chemicals and lower levels of petrochemicals to manufacture than these other products. The regulatory limits set for formaldehyde emissions are also strictest for plywood.[21]
Within this type prefer: NAF plywood, which is ranked yellow. If not possible, consider ULEF and NAUF plywood.
Similar to plywood, no added formaldehyde (NAF) medium density fiberboard (MDF) and particleboard are commonly made with binders based on isocyanates or a combination of soy-flour and synthetic resin. Both types of binder are of relatively low concern to building occupants and installers.[15]
Since both types of NAF binders are manufactured using a number of hazardous chemicals they can, however, impact workers and nearby communities. Isocyanates are potent respiratory sensitizers that are made using many hazardous chemicals, including several carcinogens.[16] The soy-based binder is made by reacting soy flour with a polyamide and epichlorohydrin resin.[17] Both the polyamide and epichlorohydrin resins use carcinogens and/or reproductive toxicants in their production.[18]
Medium density fiberboard and particleboard typically have shorter service lives than plywood.[19] They also typically require more binder than plywood. As a result, greater volumes of hazardous chemicals, including petrochemicals, are needed for these product types.
Low-density fiberboard (LDF) and high-density fiberboard (HDF) can also fall under the regulatory definition of MDF depending on how they are marketed and used, and are considered to be MDF in this guidance.
Standard medium density fiberboard (MDF) and particleboard contain binders based on formaldehyde, a carcinogen. Residual formaldehyde is gradually released from these products over time. [20]ULEF products have demonstrated that they consistently meet stricter formaldehyde emission limits than standard products at the conditions tested, so they are somewhat preferable to standard products. However, both can use urea formaldehyde binders, which react with moisture in the air and can release higher levels of formaldehyde than seen under the test conditions. They also use hazardous chemicals during manufacturing that can impact fenceline communities and workers. So, while ULEF plywood is better under some conditions during use, across its life cycle the impacts are similar to standard plywood. See the Read More section for more background on regulations and terminology.
Medium density fiberboard and particleboard typically have shorter service lives than plywood. They also typically require more binder, which means that they require higher levels of hazardous chemicals and higher levels of petrochemicals to manufacture than plywood. The regulatory limits set for formaldehyde emissions from MDF and particleboard are also not as strict as they are for plywood.[21]
Low-density fiberboard (LDF) and high-density fiberboard (HDF) can also fall under the regulatory definition of MDF depending on how they are marketed and used, and are considered to be MDF in this guidance.
Within this type prefer: NAF products. If not possible, consider ULEF and NAUF. Keep in mind that none of these are preferred product types. Consider a product type ranked yellow or green.
Supporting Information
Unless otherwise noted, product content and health hazard information is based on research done by Habitable for Common Product profiles, reports, and blogs. Links to the appropriate resources are provided.
Common Product Records Sourced
- Base Cabinetry
- High Density Fiberboard (HDF)
- High Pressure Laminate
- Hollow Core Wood Veneer Door
- Medium Density Fiberboard (MDF)
- Particleboard
- Plywood
- Polyvinyl Acetate (PVA) Interior Wood Glue
Endnotes
[1] Salthammer, Tunga, Sibel Mentese, and Rainer Marutzky. “Formaldehyde in the Indoor Environment.” Chemical Reviews 110, no. 4 (April 14, 2010): 2536–72. https://doi.org/10.1021/cr800399g; California Air Resources Board. “Proposed Airborne Toxic Control Measure to Reduce Formaldehyde Emissions from Composite Wood Products,” March 9, 2007.
Formaldehyde, CAS# 50-00-0, is listed as a carcinogen by numerous agencies, including IARC who has determined that it is carcinogenic to humans (Group 1). IARC. Chemical Agents and Related Occupations: IARC Monographs on the Evaluation of Carcinogenic Risks to Humans Volume 100F, 2012. https://publications.iarc.fr/123. In addition, formaldehyde is irritating to the ear, nose, and throat. OSHA. “OSHA Fact Sheet: Formaldehyde,” April 2011. https://www.osha.gov/sites/default/files/publications/formaldehyde-factsheet.pdf. Formaldehyde is classified as a generally accepted asthmagen by the Association of Occupational and Environmental clinics (AOEC). “AOEC - Epidemiology Tools.” Accessed April 2, 2024. http://www.aoec.org/tools.htm.
[2] California Air Resources Board. Final Regulation Order: Airborne Toxic Control Measure to Reduce Formaldehyde Emissions from Composite Wood Products, Title 17 California Code of Regulations § 93120.2 (2007). https://ww2.arb.ca.gov/sites/default/files/barcu/regact/2007/compwood07/fro-final.pdf; U.S. EPA. “Formaldehyde Emission Standards for Composite Wood Products”, 40 CFR 770, Federal Register 81, no. 238 (Dec 12, 2016): . https://www.federalregister.gov/d/2016-27987.
[3] California Air Resources Board. “Comparison of Key Requirements of CARB and U.S. EPA TSCA Title VI Regulations to Reduce Formaldehyde Emissions from Composite Wood Products,” May 2019. https://ww2.arb.ca.gov/sites/default/files/classic/toxics/compwood/comparisontable5.15.19.pdf.
[4] Salthammer, Tunga, Sibel Mentese, and Rainer Marutzky. “Formaldehyde in the Indoor Environment.” Chemical Reviews 110, no. 4 (April 14, 2010): 2536–72. https://doi.org/10.1021/cr800399g; California Air Resources Board. “Proposed Airborne Toxic Control Measure to Reduce Formaldehyde Emissions from Composite Wood Products,” March 9, 2007. https://ww2.arb.ca.gov/sites/default/files/barcu/regact/2007/compwood07/isor.pdf.
[5] California Air Resources Board. “Frequently Asked Questions: No-Added Formaldehyde and Ultra-Low Emitting Formaldehyde.” Accessed March 21, 2024. https://ww2.arb.ca.gov/resources/documents/frequently-asked-questions-no-added-formaldehyde-and-ultra-low-emitting; US EPA, OCSPP. “Frequent Questions for Regulated Stakeholders about Implementing the Formaldehyde Standards for Composite Wood Products Act.” Overviews and Factsheets, July 26, 2016. https://www.epa.gov/formaldehyde/frequent-questions-regulated-stakeholders-about-implementing-formaldehyde-standards.
[6] California Air Resources Board. Final Regulation Order: Airborne Toxic Control Measure to Reduce Formaldehyde Emissions from Composite Wood Products, Title 17 California Code of Regulations § 93120.2 (2007).https://ww2.arb.ca.gov/sites/default/files/barcu/regact/2007/compwood07/fro-final.pdf; U.S. EPA. “Formaldehyde Emission Standards for Composite Wood Products”, 40 CFR 770, Federal Register 81, no. 238 (Dec 12, 2016): . https://www.federalregister.gov/d/2016-27987; ASTM International. “Standard Test Method for Determining Formaldehyde Concentrations in Air and Emission Rates from Wood Products Using a Large Chamber.”https://www.astm.org/e1333-10.html; ASTM International. “Standard Test Method for Determining Formaldehyde Concentrations in Air from Wood Products Using a Small-Scale Chamber.” https://www.astm.org/d6007-02.html.
[7] Salthammer, Tunga, Sibel Mentese, and Rainer Marutzky. “Formaldehyde in the Indoor Environment.” Chemical Reviews 110, no. 4 (April 14, 2010): 2536–72. https://doi.org/10.1021/cr800399g.
[8] California Air Resources Board. “Frequently Asked Questions: Applicable Products.” Accessed April 2, 2024. https://ww2.arb.ca.gov/resources/documents/frequently-asked-questions-applicable-products.
[9] California Environmental Protection Agency. “Frequently Asked Questions,” February 2016. https://www.arb.ca.gov/toxics/compwood/implementation/faq.htm.
[10] “Environmental Impacts of Natural Gas,” Union of Concerned Scientists, June 19, 2014, https://www.ucsusa.org/resources/environmental-impacts-natural-gas.; Garcia-Gonzales, Diane A., Seth B.C. Shonkoff, Jake Hays, and Michael Jerrett. “Hazardous Air Pollutants Associated with Upstream Oil and Natural Gas Development: A Critical Synthesis of Current Peer-Reviewed Literature.” Annual Review of Public Health 40, no. 1 (2019): 283–304. https://doi.org/10.1146/annurev-publhealth-040218-043715; Deziel, Nicole C. “Environmental Injustice and Cumulative Environmental Burdens in Neighborhoods Near Oil and Gas Development: Los Angeles County, California, and Beyond.” American Journal of Public Health 113, no. 11 (November 2023): 1173–75. https://doi.org/10.2105/AJPH.2023.307422; Deziel, Nicole C., Cassandra J. Clark, Joan A. Casey, Michelle L. Bell, Desiree L. Plata, and James E. Saiers. “Assessing Exposure to Unconventional Oil and Gas Development: Strengths, Challenges, and Implications for Epidemiologic Research.” Current Environmental Health Reports 9, no. 3 (September 1, 2022): 436–50. https://doi.org/10.1007/s40572-022-00358-4.
[11] Gonzalez, David J. X., Anthony Nardone, Andrew V. Nguyen, Rachel Morello-Frosch, and Joan A. Casey. “Historic Redlining and the Siting of Oil and Gas Wells in the United States.” Journal of Exposure Science & Environmental Epidemiology, April 13, 2022, 1–8. https://doi.org/10.1038/s41370-022-00434-9; Berberian, Alique G., Jenny Rempel, Nicholas Depsky, Komal Bangia, Sophia Wang, and Lara J. Cushing. “Race, Racism, and Drinking Water Contamination Risk From Oil and Gas Wells in Los Angeles County, 2020.” American Journal of Public Health 113, no. 11 (November 2023): 1191–1200. https://doi.org/10.2105/AJPH.2023.307374; Chan, Marissa, Bhavna Shamasunder, and Jill E. Johnston. “Social and Environmental Stressors of Urban Oil and Gas Facilities in Los Angeles County, California, 2020.” American Journal of Public Health 113, no. 11 (November 2023): 1182–90. https://doi.org/10.2105/AJPH.2023.307360; Tim Donaghy and Charlie Jiang, “Fossil Fuel Racism: How Phasing Out Oil, Gas, and Coal Can Protect Communities,” April 13, 2021, https://www.greenpeace.org/usa/reports/fossil-fuel-racism.
[12] Vallette, Jim. “Chlorine & Building Materials Project: Phase 1 Africa, The Americas, and Europe.” Healthy Building Network, July 2018. https://habitablefuture.org/resources/chlorine-building-materials-project-phase-1-africa-the-americas-and-europe/; Vallette, Jim. “Chlorine & Building Materials Project: Phase 2 Asia Including Worldwide Findings,” March 2019. https://habitablefuture.org/resources/chlorine-building-materials-project-phase-2-asia-including-worldwide-findings.
[13] Zhang, Mengmei, Alfons Buekens, Xuguang Jiang, and Xiaodong Li. “Dioxins and Polyvinylchloride in Combustion and Fires.” Waste Management & Research 33, no. 7 (July 1, 2015): 630–43. https://doi.org/10.1177/0734242X15590651; Avakian Maureen D, Dellinger Barry, Fiedler Heidelore, Gullet Brian, Koshland Catherine, Marklund Stellan, Oberdörster Günter, et al. “The Origin, Fate, and Health Effects of Combustion by-Products: A Research Framework.” Environmental Health Perspectives 110, no. 11 (November 1, 2002): 1155–62. https://doi.org/10.1289/ehp.021101155.
[14] Healthy Building Network, and Perkins+Will. “Healthy Environments: Understanding Antimicrobial Ingredients in Building Materials,” March 2017. https://habitablefuture.org/resources/healthy-environmentsunderstanding-antimicrobial-ingredients-in-building-materials.
[15] Isocyanates are a concern to building occupants and installation teams when they are in wet-applied products, like spray foam insulation, because they are highly reactive and potent respiratory sensitizers. When composite wood containing isocyanate-based binders leaves a manufacturing facility, these reactive molecules have mostly combined with each other and with the wood to form large molecules that do not share the same concerns; Frazier, Charles E. “Isocyanate Wood Binders.” In Handbook of Adhesive Technology, 2:383–91. Marcel Dekker New York, 2003.
[16] HBN/EEFA/NRDC. “Chemical and Environmental Justice Impacts in the Life Cycle of Building Insulation: Case Study on Isocyanates in Spray Polyurethane Foam.” Energy Efficiency for All, September 2022. https://informed.habitablefuture.org/resources/research/18-case-study-on-isocyanates-in-spray-polyurethane-foam.
[17] Spayde, Timothy F., Chris J. Watt, and Steven Pung. Cold pressing process for polyamide epichlorohydrin (PAE) based wood adhesive. United States US8470124B1, filed August 9, 2011, and issued June 25, 2013. https://patents.google.com/patent/US8470124B1/en.
[18] Epichlorohydrin is classified as having known or suspected carcinogenicity on over a dozen hazard lists. The National Institute for Occupational Safety and Health (NIOSH) classifies it as an occupational carcinogen. Centers for Disease Control and Prevention. “CDC - Immediately Dangerous to Life or Health Concentrations (IDLH): Epichlorohydrin - NIOSH Publications and Products,” November 2, 2018. https://www.cdc.gov/niosh/idlh/106898.html. It is also classified as a reproductive toxicant by the State of California: OEHHA. “Epichlorohydrin.” Text. California Office of Environmental Health Hazard Assessment, July 23, 2015. https://oehha.ca.gov/proposition-65/chemicals/epichlorohydrin.
Diethylenetriamine [CASRN 111-40-0], a monomer in the synthesis of the polyamide resin, is classified as a suspected reproductive toxicant under the GHS classification systems of New Zealand and Japan (Category 2 and Category 1B respectively): Environmental Protection Authority. “Chemical Classification and Information Database (CCID).” Accessed April 2, 2024. https://www.epa.govt.nz/database-search/chemical-classification-and-information-database-ccid/view/EB07CFC3-E1E7-4577-894F-87F4DD9E9498; National Institute of Technology and Evaluation. “NITE - Chemical Management Field - GHS Information.” Accessed April 2, 2024. https://www.nite.go.jp/chem/english/ghs/m-nite-111-40-0e.html.
[19] Parsons School of Design. “Healthy Materials Lab | Healthier Cabinetry Guide.” Healthy Materials Lab. Accessed April 2, 2024. https://healthymaterialslab.org/tool-guides/healthier-cabinetry-guide.
[20] Salthammer, Tunga, Sibel Mentese, and Rainer Marutzky. “Formaldehyde in the Indoor Environment.” Chemical Reviews 110, no. 4 (April 14, 2010): 2536–72. https://doi.org/10.1021/cr800399g.
[21] The emissions standards are: 0.05 ppm for hardwood plywood, 0.09 ppm for particleboard, 0.11 ppm for MDF, and 0.13 ppm for thin MDF. Products made with ULEF resins have lower emissions thresholds and must demonstrate that they consistently emit formaldehyde at or below these lower thresholds. See the regulations for more details: California Air Resources Board. Final Regulation Order: Airborne Toxic Control Measure to Reduce Formaldehyde Emissions from Composite Wood Products, Title 17 California Code of Regulations § 93120.2 (2007). https://ww2.arb.ca.gov/sites/default/files/barcu/regact/2007/compwood07/fro-final.pdf; U.S. EPA. “Formaldehyde Emission Standards for Composite Wood Products”, 40 CFR 770, Federal Register 81, no. 238 (Dec 12, 2016): . https://www.federalregister.gov/d/2016-27987.
Last updated: April 22, 2024