Pacific Northwest Baseline Specification Review
Baseline Specification Review Home
- 12 Urban-Large City
- 9 Non-profit
- 3 Not provided
- 10 New Construction
- 2 Rehab
Cabinetry & Millwork
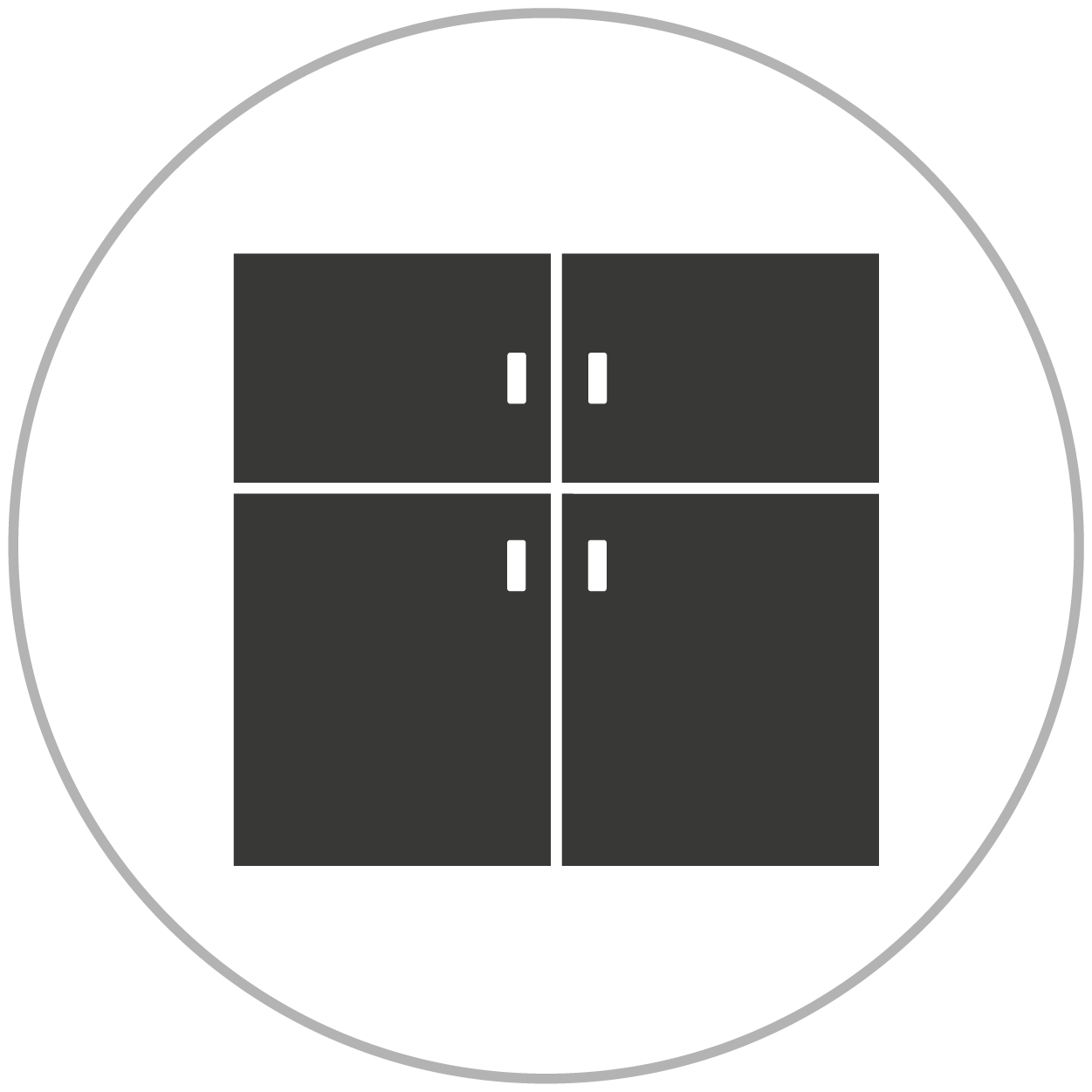
- All the projects had requirements for cabinets limiting formaldehyde based binders or formaldehyde emissions.
- About 20% of the projects specified CA 93120/CARB Phase II compliant.
- About 65% of projects specified composite wood products that contain no urea formaldehyde.
- A majority of projects specified cabinet manufacturers, but did not include specific product lines.
- Nearly all projects specified cabinets with a factory finish.
- About 20% of projects specified a laminate (HPL or melamine) or thermofoil finish for exterior faces, with an additional 35% specifying laminate only for interior surfaces.
- All projects specified wood trim/base in at least some part of the units.
- Most projects specified rubber wall base somewhere. None specified vinyl wall base.
- About 45% of projects specified MDF for some trim or as an alternative to wood in at least some places.
- 60% of projects that allowed or specified MDF required that it be free of urea-formaldehyde or formaldehyde-free.
Doors
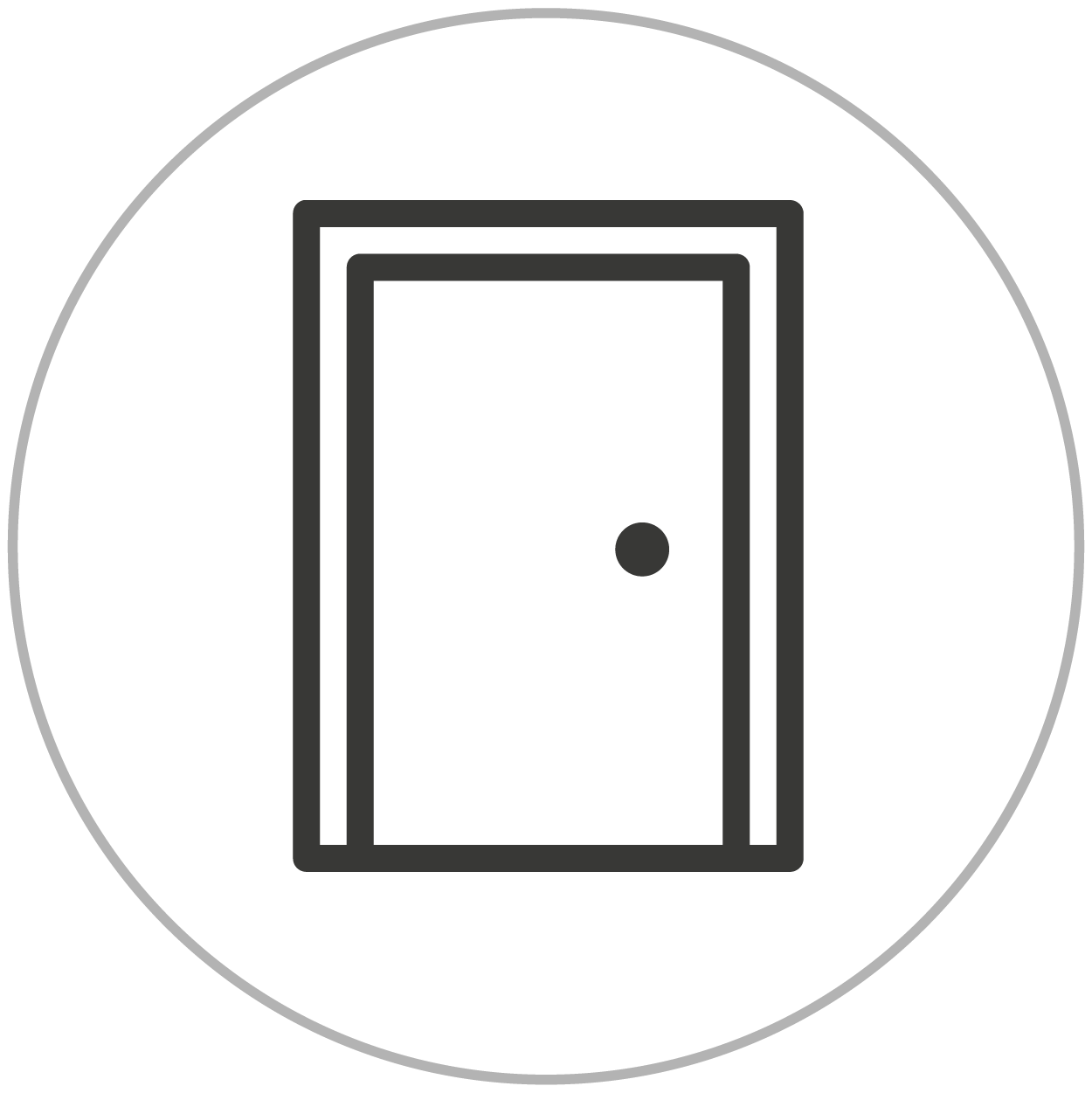
- About 90% of projects specified doors with a composite core, and about 25% specified hollow core doors with a composite face.
- About 60% of projects that included wood doors with composite core or facing specified no urea formaldehyde - one project further specified that all components be formaldehyde-free.
- Only 2 projects specified a particular product or series; the others provided general information about which materials should be used and often included approved manufacturers.
- Over 80% of projects specified factory finished wood doors with an additional 10% specifying a combination of factory finished and site finished.
Countertops
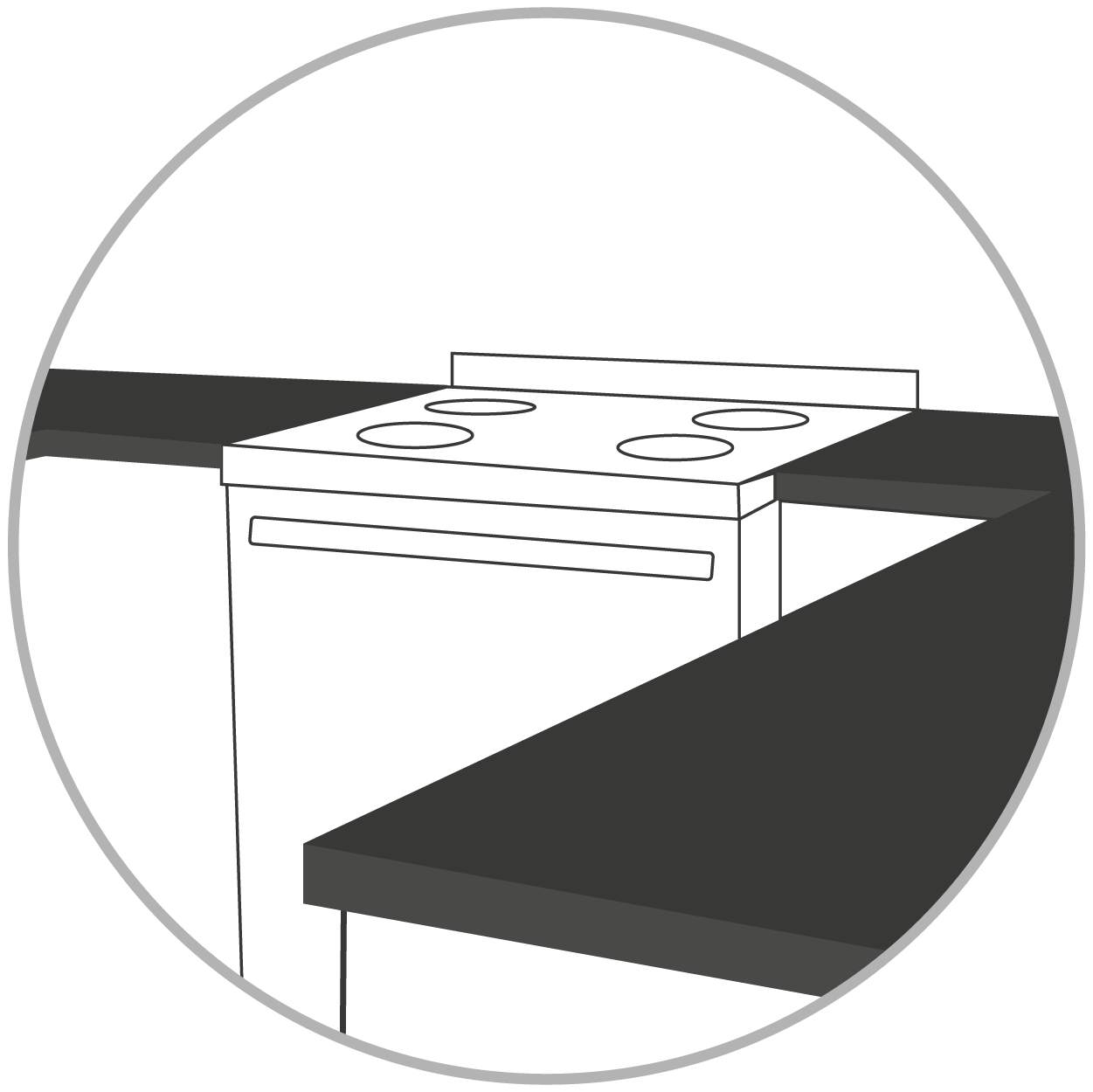
- Plastic laminate dominates in the Pacific Northwest affordable housing projects reviewed - it was specified in about 90% of kitchens and about 70% of bathrooms.
- One project avoided plastic laminate all together, specifying solid surface countertops in both kitchen and bath.
- 25% specified quartz or solid surface as an alternate countertop to laminate.
- Almost 65% of projects specified substrates with no urea formaldehyde, and about 10% specified formaldehyde-free materials.
Drywall
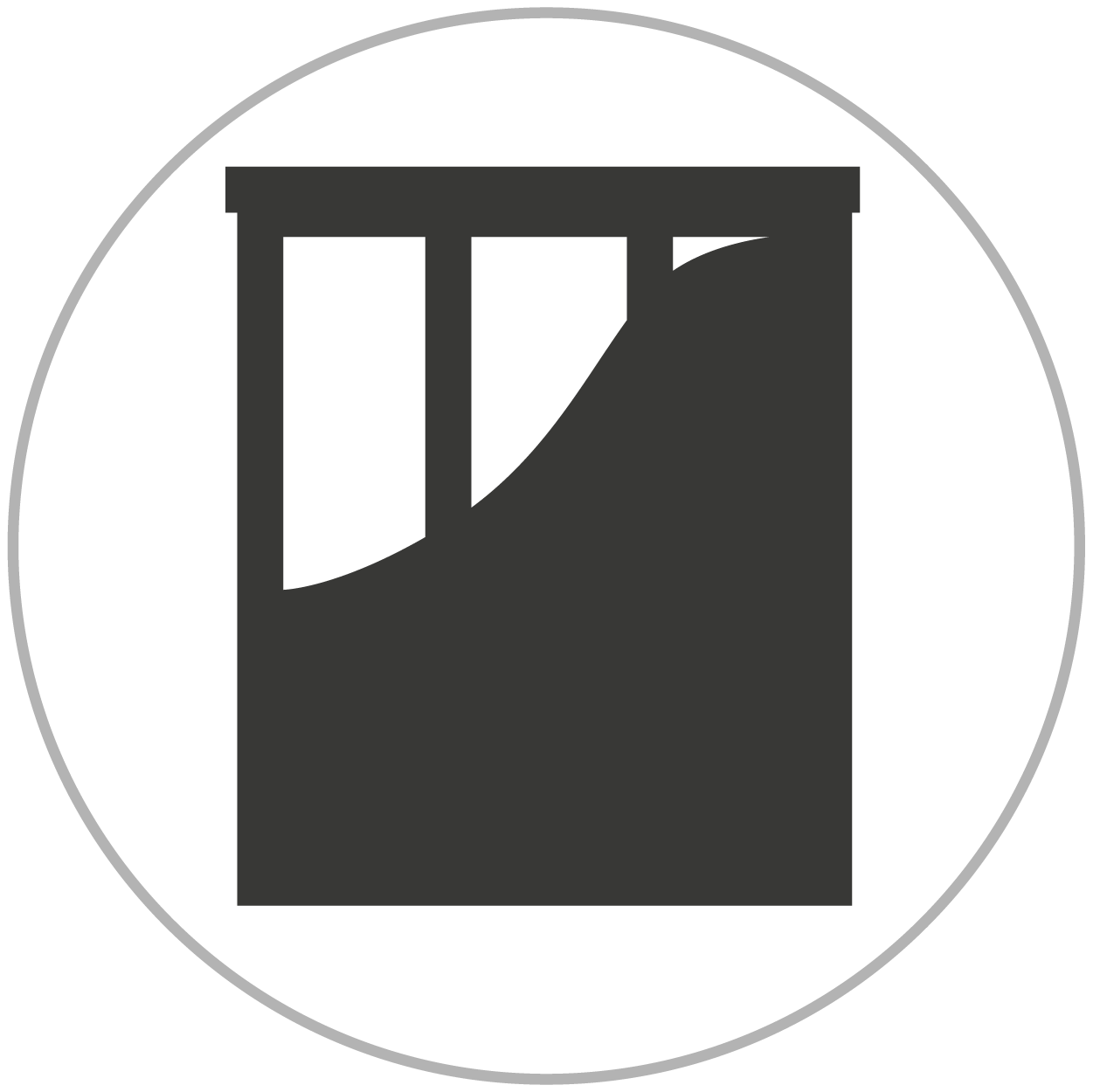
- One project had a specific recycled content requirement that called for either 10% post-consumer or 95% pre-consumer content - the latter of which would mean synthetic gypsum was definitely used. The Pacific Northwest is currently unique in their local access to gypsum boards with post-consumer content in the core.
- No projects specified natural gypsum as a requirement.
- Almost three quarters of projects specified wall and/or ceiling texture.
Flooring
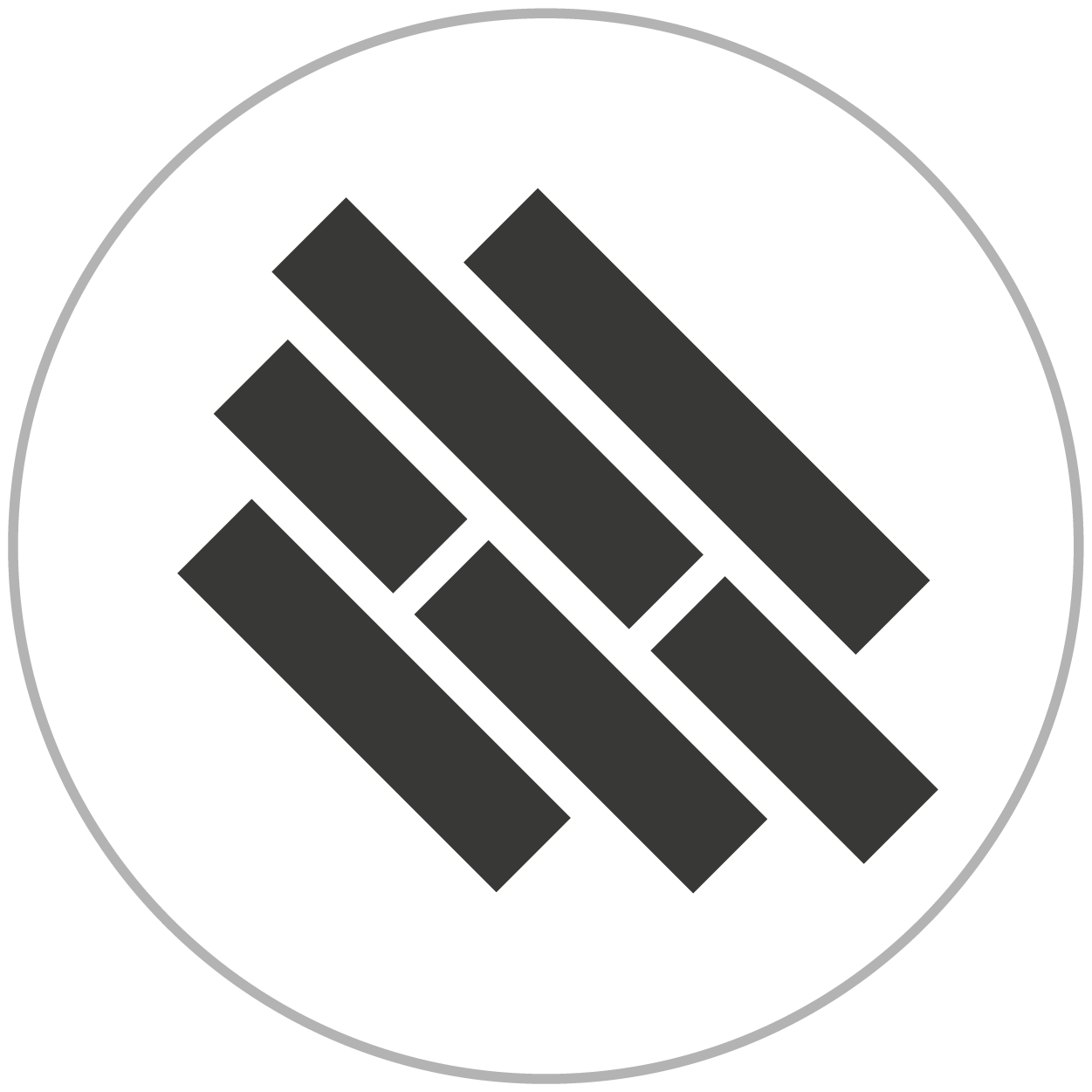
- All projects specified vinyl flooring somewhere in the building, with the majority specifying it somewhere in the unit.
- Over 90% of projects specified carpeting. About 80% of these required Green Label or Green Label Plus certification. (This industry-backed certification only covers some VOC emissions; some hazardous VOC and all non-VOC chemicals are excluded.) One project specified Cradle to Cradle Bronze.
- Other flooring products specified include ceramic tile, laminate, and linoleum. Polyolefin sheet flooring was listed as an alternate to vinyl sheet in one project.
- Over 80% of projects set VOC content limits on flooring adhesives consistent with SCAQMD 1168 requirements.
- A wide variety of carpet pad was specified: 40% of projects specified fiber carpet pad. Other types specified include rubber, prime polyurethane, and rebond.
Insulation
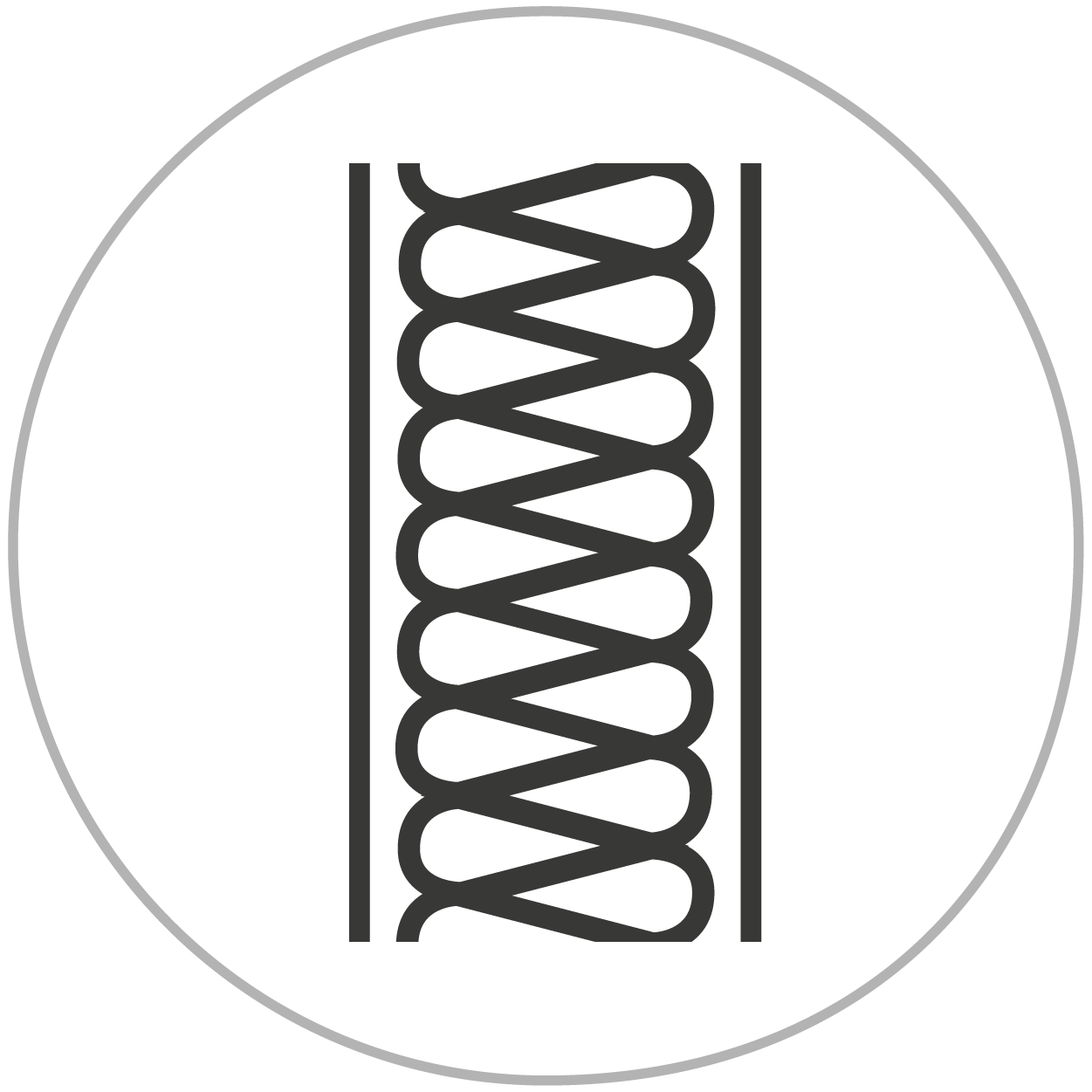
- All projects specified use of fiberglass batt insulation.
- About 35% of projects specified that fiberglass batts be formaldehyde-free and about 20% specified they have no urea-formaldehyde. As of October 2015, all residential fiberglass batt insulation made in the U.S. is formaldehyde-free.
- Over 60% of projects specified blown fiberglass insulation for exterior walls.
- Over 60% of projects list polyurethane spray foam (either 1- or 2-part) for sealing gaps or miscellaneous voids. One project specified a 2-part latex-based spray foam product for air sealing.
Paint
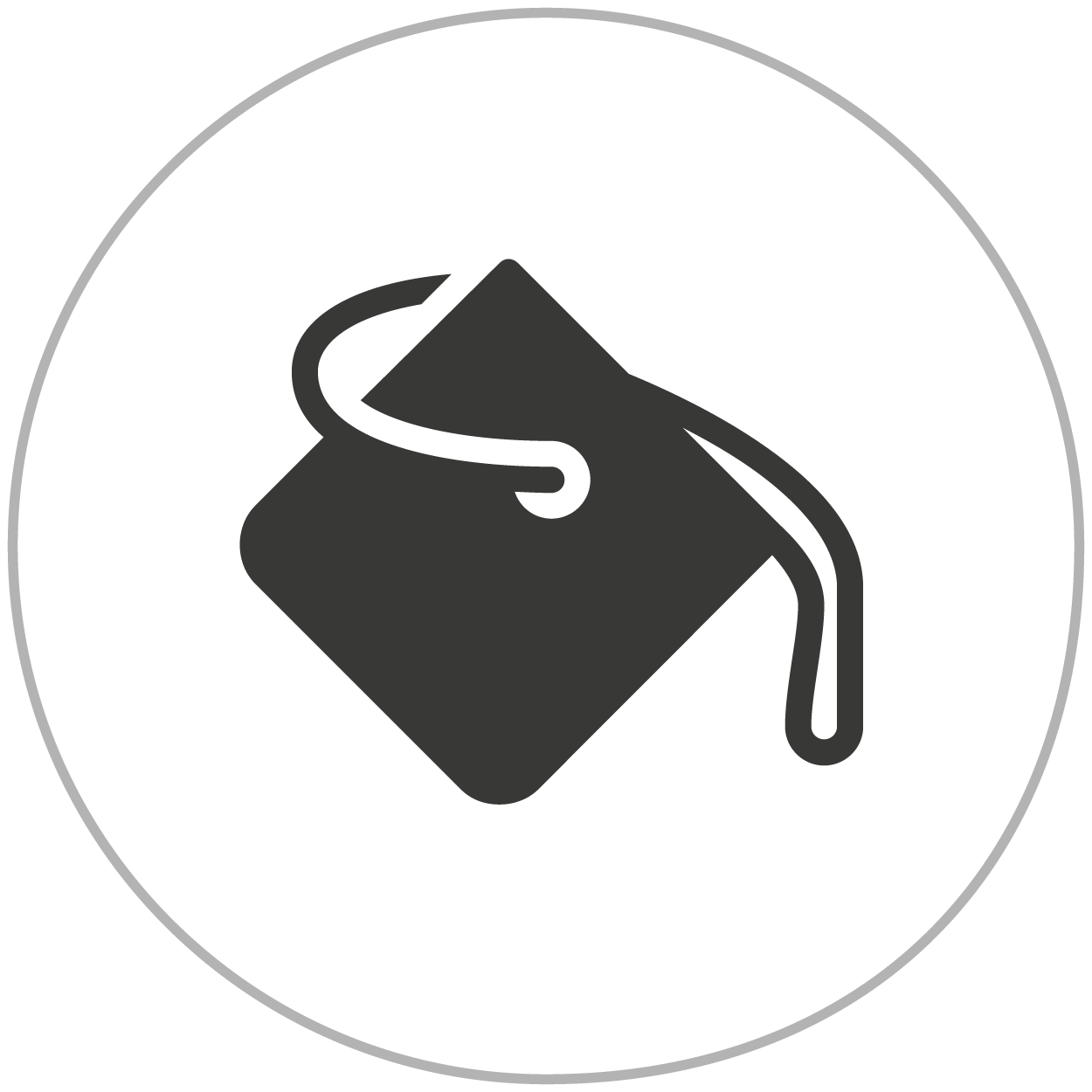
- All projects reviewed specified a VOC content requirement.
- All projects that specified flat paint, specified that it have <50 g/L VOCs. Most of these also specified a VOC limit of 100 g/L, including colorant added at the point of sale.
- Over 60% of projects specified non-flat paint limited to <50 g/L VOCs. Most of these also specified a VOC limit of 100 g/L, including colorant added at the point of sale.
- No specific VOC requirements for tints were indicated except as noted above regarding VOC limits including colorant at point of sale.
- About 20% of the projects specified paint that meets an older, less strict version of the Green Seal-11 standard.